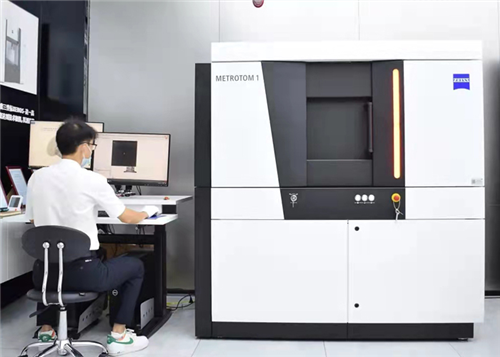
在半導體產業向3nm制程突進的今天,一顆直徑僅300毫米的晶圓上集成了超千億個晶體管,任何微米級缺陷都可能導致整條生產線的良率崩塌。德國蔡司工業CT機憑借其納米級檢測精度,正在重塑半導體產業鏈的質量控制體系,成為晶圓廠、封裝測試企業不可或缺的“數字顯微鏡”。
穿透硅基的“X光視覺”
傳統聲學顯微鏡(SAM)在檢測芯片封裝空洞時,只能獲取二維截面圖像。蔡司METROTOM 1500工業CT機通過錐束X射線技術,可實現三維斷層掃描,其核心優勢在于:
空間分辨率突破:在1500mm測量范圍內達到0.5μm體素精度,足以分辨7nm制程芯片的金屬互連線寬變化
多材質穿透能力:采用雙能X射線源,可穿透10層堆疊的硅基板與金屬層,完整呈現TSV硅通孔結構
動態成像技術:每秒捕獲1600幀投影數據,實現封裝過程實時監測,將翹曲檢測效率提升8倍
在臺積電的3D Fabric封裝產線,該設備成功檢測出0.3μm的銅柱凸點偏移,避免批量性電性失效。更關鍵的是,其CT值標準化功能可自動區分空氣空洞、金屬殘留與有機物污染,將缺陷分類準確率提升至99.7%。
晶圓級檢測的革命性突破
在晶圓制造環節,蔡司Xradia 620 Versa系統展現出三大技術突破:
缺陷定位精度:通過相襯成像技術,可檢測出埋藏在300μm硅層下方的0.1μm級晶體缺陷
多尺度分析:從晶圓級宏觀形貌到原子級晶格結構,實現跨尺度檢測數據無縫銜接
大數據處理:配套的Dragonfly Pro軟件可每小時處理1TB掃描數據,生成包含3000個參數的缺陷圖譜
在英特爾俄勒岡工廠的應用中,該系統提前3個月預警光刻膠殘留導致的金屬線斷路風險,使先進制程的良率提升2.3個百分點。這種預測性維護能力,正成為晶圓廠降低制造成本的關鍵。
封裝失效分析的“數字孿生”
蔡司工業CT機在先進封裝領域的應用,正在重構失效分析流程:
虛擬解構:通過CT數據重建,可無損拆解BGA、CSP等復雜封裝結構,獲取焊點三維形貌
熱應力模擬:結合ANSYS Workbench,對掃描數據進行熱-力耦合分析,預測-55℃~150℃溫變下的可靠性
逆向工程:將掃描數據直接轉換為CAD模型,使封裝設計迭代周期縮短60%
在日月光集團的案例中,技術人員通過CT掃描發現某5G芯片封裝體的熱應力集中區,經結構優化后使產品通過MIL-STD-883H軍用標準測試。這種“檢測-分析-優化”的閉環,正推動封裝技術向2.5D/3D堆疊快速演進。
未來技術演進圖譜
隨著EUV光刻技術普及,半導體檢測正面臨新挑戰。蔡司已啟動“CT 2.0”研發計劃:
AI輔助檢測:基于百萬級缺陷數據庫訓練的神經網絡,實現缺陷的自動識別與分級
量子增強成像:探索量子傳感器與CT技術的融合,將信噪比提升10倍以上
云檢測平臺:構建基于5G的分布式檢測網絡,實現全球工廠間的檢測數據實時共享
當半導體產業進入埃米時代,蔡司工業CT機已不僅是檢測設備,更是質量控制的智能中樞。從晶圓制造到封裝測試,從失效分析到工藝優化,這臺“透視眼”正在重塑半導體產業的價值鏈。隨著AI與量子技術的持續賦能,未來的CT檢測或將實現原子級的實時監控,為摩爾定律的延續開辟新路徑。