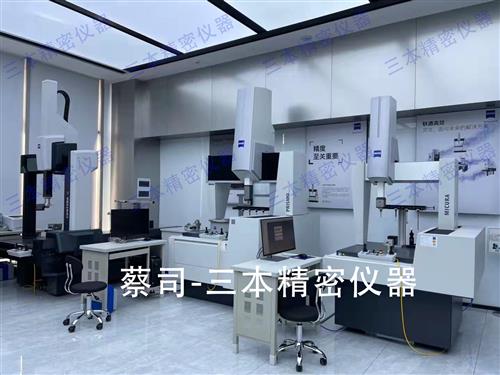
在精密制造領域,測量精度直接影響產品質量與性能。作為全球光學與光電技術先驅,蔡司自1973年推出全球首臺三坐標測量機UMM500以來,始終以突破性的技術重新定義工業測量標準。本文將深度解析蔡司三坐標測量機的技術內核與應用價值,揭示其如何成為現代制造業的質量守護者。
百年技術積淀,鑄就測量精度新標桿
蔡司三坐標測量機的技術傳承可追溯至1846年,歷經179年精密制造經驗沉淀,其測量精度始終引領行業。以XENOS機型為例,在1立方米測量空間內可實現0.3μm的超高精度,這一數據相當于人類頭發絲直徑的1/200。這種極致精度源于多項獨家技術:采用零膨脹玻璃陶瓷材質的懸浮式光柵尺,配合四面環抱氣浮軸承技術,使設備在高速運動中仍能保持納米級穩定性;工業陶瓷導軌的應用,有效抵御溫度波動對測量結果的影響,確保檢測數據的絕對可靠。
在測頭系統領域,蔡司RDS旋轉測頭技術實現突破性創新。CONTURA機型配備的2.5°步距角旋轉測頭,可生成20736個測量點位,相比傳統測頭檢測效率提升300%。搭配Thermo Fit碳纖維測針,既能深入檢測深腔結構,又能避免材料熱脹冷縮引發的測量誤差。這種技術組合使發動機葉片、醫療器械等復雜零部件的檢測成為可能,某航空企業應用后,葉片檢測效率提升40%,廢品率下降25%。
智能軟件賦能,重構工業檢測流程
蔡司自主研發的CALYPSO測量軟件,開創了"所見即所測"的智能檢測新模式。該軟件基于CAD原理開發,支持在三維模型上直接標注公差并生成檢測程序,將編程時間從數小時縮短至幾分鐘。在汽車變速箱齒輪檢測中,軟件可自動識別齒面輪廓偏差,精度達0.001mm,幫助企業將齒輪噪音問題檢測效率提升60%。
針對新能源電池模組檢測,蔡司三坐標配備光學掃描測頭,采用結構光測量技術,單次掃描即可獲取百萬級點云數據。某動力電池企業應用后,模組平面度檢測時間從2小時壓縮至15分鐘,檢測數據完整度提升90%。這種非接觸式檢測方案,有效解決了傳統接觸測量可能造成的工件損傷問題。
全行業覆蓋,構建質量保障生態
在航空航天領域,蔡司四軸聯動掃描技術可同時檢測渦輪葉片的氣動曲面與安裝孔位。某航空發動機廠商應用該技術后,葉片檢測合格率從85%提升至99.2%,單臺發動機檢測時間縮短50%。針對新能源汽車電機軸檢測,蔡司開發了專用夾具與檢測算法,可同步完成軸徑、圓度、同軸度等12項參數檢測,檢測精度達0.5μm。
在模具制造行業,蔡司的工業CT無損檢測功能,可透視檢測鋁壓鑄件內部縮松缺陷。某汽車模具企業應用后,模具返修率下降35%,生產周期縮短20%。針對精密電子元器件檢測,設備可捕捉0.02mm²的微小焊點缺陷,為5G通信設備質量保駕護航。
服務生態升級,賦能產業數字化轉型
蔡司不僅提供硬件設備,更構建了完整的質量保障解決方案。其全國售后服務網絡可實現24小時快速響應,某醫療器械企業在深夜遇到檢測異常時,工程師通過遠程診斷系統,2小時內完成故障定位與解決方案輸出。針對職業教育領域,蔡司開發了虛擬測量教學系統,通過數字孿生技術模擬真實檢測場景,已助力全國50余所院校培養專業檢測人才。
從德國奧伯科亨到中國制造現場,蔡司三坐標測量機正以0.3μm的精度追求,重塑工業測量的價值邊界。在智能制造2025戰略背景下,這種將百年光學智慧與數字技術深度融合的檢測方案,將成為中國制造業邁向全球價值鏈中高端的關鍵支撐。當蔡司三坐標的測頭輕觸工件表面,觸碰的不僅是金屬與數據,更是中國制造的質量未來。